This article is adapted from a presentation made at the 2017 ICF Summit titled “Building Your Construction Business with Disaster-Resistant ICF Structures.” Part I appeared in the July 2019 issue.
Back in the 1990s, when I started talking to people about concrete homes and ICF, they didn’t understand it, and those that did thought the cost would be prohibitive.
Over a few short years, though, I went from selling a couple truckloads of forms to consistently selling more than 100 truckloads of forms per year. I soon became the top ICF distributor for three years running before shifting to a different brand, and shortly I became their top distributor for multiple years as well.
After having built more than 4,000 homes and 100 commercial buildings, I’m convinced ICF are the single most important building material of our time for the construction of disaster-resistance homes and businesses.
The True Cost Of Disasters
Over the past 10 years, the United States has averaged more than 1,000 tornadoes annually, causing 227 fatalities and $1.1 billion in property damage each year. That’s just the tornadoes.
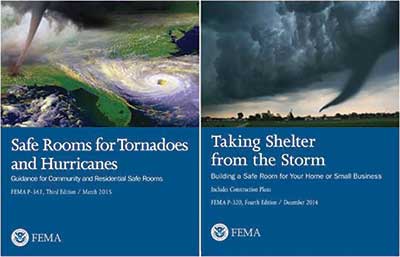
U.S. government publications like these show how ICFs can create high performance cost-effective storm shelters.
The average yearly monetary loss from hurricanes in the United States is $10 billion; that’s from data going back 106 years. Obviously, some years have none, but several years recently have seen losses as high as $157 billion from a single event.
Fires are another major danger. In 2015, there were over 1.34 million fires, leading to 3,280 deaths, 15,700 injuries, and $14.3 billion in property damage.
It’s time to build structures that are safer and more disaster-resistant. I don’t know why codes are not stiffer, but that does give us as an industry a chance to sell our customers on the benefits of upgrading to a better, stronger, safer structure.
Storm Shelters
On May 3, 1999, a large and extraordinarily powerful F5 tornado struck Oklahoma City. It’s calculated to still be the most powerful tornado to ever hit the United States, with wind speeds recorded in excess of 300 mph. It laid a path of destruction more than 100 miles long through Oklahoma, destroying dozens of neighborhoods and communities. This is what really compelled me to focus on my ICF business.
Shortly after the storm, I got involved with FEMA in Oklahoma City. There were only two storm shelters in the path of the tornado. Both of them survived, as did the occupants. One was a concrete structure; the other was metal. Every other structure around them for some distance was destroyed and leveled to the ground.
I learned FEMA was planning to put out a publication titled Taking Shelter from the Storm which would include plans for storm shelters. I got the ICF manufacturers involved with FEMA’s engineers, and—in conjunction with the governor’s office in Oklahoma—we designed a safe room that met FEMA’s calculations. This was included with that publication (along with several other designs using alternative materials). This really boosted the entry of ICF in the storm shelter business. After that, we were selling storm shelters as fast as we could put them up.
Texas Tech University is very involved in wind speed testing and the damage that can be caused by flying debris. They have a cannon that will propel a 2×4 into a wall sample at more than 100 mph, which imitates the dangerous conditions in these wind events. The only wall systems that withstood projectiles like this were an ICF wall and a solid concrete wall. Even the CMU (concrete block) wall failed when projectile speeds exceeded 90 mph.
ICFs are among the safest and strongest materials for storm shelter construction. Additionally, they can be built above-grade, as part of the home, and the space can be used by the occupants as part of their normal lifestyle.
Below-ground structures can be pretty dangerous. They’re difficult to access. They can become flooded with rain, or debris can collapse on top of them, trapping the occupants.
Build the safe room as a room in the home. It’s easy to get to, and it’s not wasted space. You can use it. Frequently it doubles as a walk-in closet. If the weather threatens, just put the kids to sleep in there. It’s so much better than a dark, damp, buried shelter in the backyard or under a car.
Fires
I’ve already noted that fires and wildfires are one of the largest sources of destruction in the United States. Again, ICFs are one way to provide protection for owners and their belongings. Obviously, in order to do this, the roof and exterior finishes must also be fire-resistant.
Testing proves that even a CMU (concrete block) wall will fail when projectile speeds exceed 90 mph.
All of the major ICF brands have undergone firewall testing. This is a 10×10-foot wall segment is used with a six-inch concrete core. After being made, it sits for six to nine months to get the moisture content of the concrete down. Then, the wall is placed in a kiln, with a huge natural gas fire roaring on one side of the wall for four hours straight. The temperature exceeds 2,000 degrees. Then, the furnace is turned off, and the wall is immediately hit with high pressure water from a fire hose for four or five minutes, as if firemen were trying to put out a real fire.
An ICF wall, visible at the right, is fire-tested in a 2,000-degree furnace for four hours, then doused with a firehose.
The massive temperature change leads to some spalling, but it’s not very deep. After the fire hose test, the wall is then loaded to 5,000 lbs./lineal ft. to ensure it’s still structurally sound. After my product was tested, I asked them to increase the load as much as they could. The wall was taken all the way to 12,000 lbs./lineal ft., which was as much pressure as the machine could apply, with no deflection.
Cost Considerations
How much more does it cost to achieve this level of safety? A comprehensive study was done a few years back, and was published under the title Fire Safe Construction Cost Comparison Study. It looked at five different types of construction: conventional wood framing, light gauge steel framing, load bearing concrete masonry, precast concrete, and ICFs.
Independent building science reports have confirmed that ICF is the most cost-effective way to build fire-resistant homes.
The bottom line is that by utilizing a compartmentalized construction method, building with ICFs increased the overall cost less than five percent compared to the cheaper alternatives. Most commercial buildings have more in their budget overruns than it would cost to build with ICF. Now, this doesn’t take into consideration other factors. Most owners will find that they recoup that small extra cost within a very short period of time in energy savings alone. So ICFs are very affordable, and offer great benefit to the property owners.
Other Considerations
We’ve seen that ICFs can survive fire and wildfire, hurricanes and tornadoes. Now, there are many things that you may need to do in order to have the roof survive either a fire or a 200 mph wind. You’re going to need to build a quality roof structure, and will probably need to upgrade the windows as well. A few builders are offering concrete decks and roof systems that totally encapsulate the structure with disaster-resistant materials.
ICF homes have proven to withstand tremendous storms with minimal damage, such as this Cayman Island home after Hurricane Ivan.
In addition to the natural disasters we’ve already covered, I should mention that ICFs can also survive earthquakes, mold, mildew, termites, and automobile collisions.
ICFs also offer a number of other benefits to the occupant in addition to safety, including improved air quality and temperature control, predictable energy costs, and a safe and quiet environment. I like to point out to my clients that it is cheaper from Day One to build and live in an ICF structure than it is to build and live in a stick frame or CMU structure. This happens because the significant energy savings can be applied to the small increase in monthly mortgage costs, which pays the owner back the entire cost of the upgrade. An ICF structure uses 50% less energy than one built with high-quality 2×6 framed walls.
Mike Garrett is the founder of BuildBlock Building Systems, a leading provider of ICFs. Prior to founding that company in 2004, he was the leading distributor for two other ICF brands. He retired from the industry in 2019.